Back to the future — with seaweed







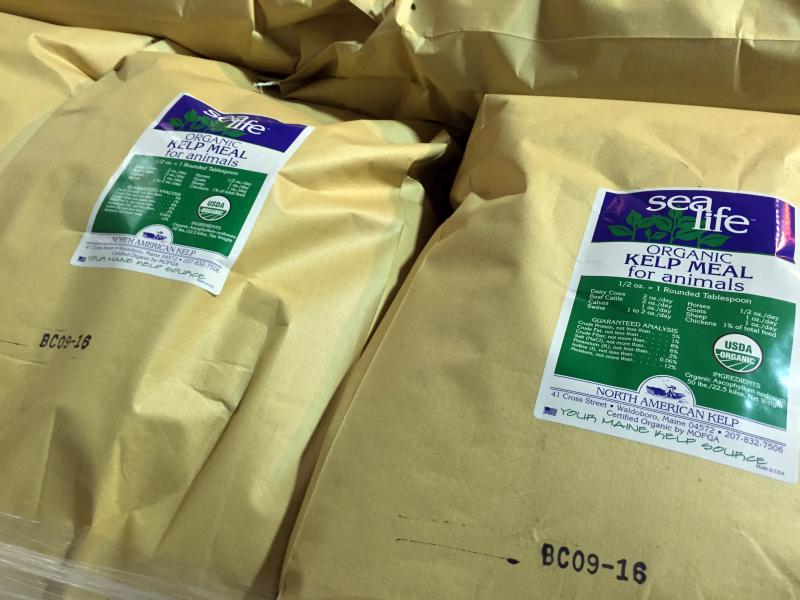








A story ran in the August 4, 1972 issue of the Portland Press Herald with the headline: “A Future for Seaweed?”
The answer is yes.
The story was about a young entrepreneur, Robert Morse, who started a seaweed processing business, the Samoset Algae Co., in 1971.
Originally from Marlborough, Massachusetts, Morse is a merchant marine engineer who sailed in the Vietnam era. His family used to spend every August in Boothbay Harbor on their schooner. In 1962 his parents purchased a home on Samoset Road.
One of the first members of Maine's Organic Farmers and Gardeners Association, Morse became interested in the benefits of seaweed when he planted his first garden. “I wanted to grow an organic garden and I saw an ad for liquid seaweed. There was a picture of the Norwegian coast, and when I got their brochure, it looked like my front yard, the Sheepscot River. I thought, 'I could do that.'”
It wasn't an entirely foreign concept to Morse. “When I was 12, on Cape Cod, my cousins were harvesting Irish sea moss. My first job was pulling the starfish and mussels out of sea moss.”
His products are now sold nationwide.
Now North American Kelp, the company is located in Waldoboro where kelp, harvested off the coast of Maine, is processed.
On March 7, Morse's 30,000 square foot processing plant was buzzing with activity. A 25-ton harvest of seaweed had been brought in.
According to the Portland Press Herald story, in 1972 the seaweed was being cut from the rocks by a couple of young employees, Pete Thayer and Bob Thompson. The seaweed was hauled in a dory, then dried outside in the sun. Once dry, the seaweed was ground up and made into a seaweed meal.
The process of drying the seaweed, or kelp, has gotten a little more complicated over the past 44 years.
Well, actually a lot more.
Instead of sunshine, Morse now uses wood pellets as fuel for drying. “They burn as clean as natural gas,” he said. “We've used Maine wood pellets for seven years. We're not buying any foreign fuel.”
The seaweed is mechanically harvested, using seven owner-operated mechanical harvesters fishing for seaweed in bays and inlets, from Eastport to Casco Bay.
Once the kelp has been trucked to the plant, it is conveyed to a large, rotating wood-fired drum to dry. Four pounds of wet seaweed will make one pound of dry.
The dried kelp meal is then blown into 2,500-pound “bulk bags,” and eventually winds up in 50-pound bags for distribution to farms and grain companies to be used as an organic feed supplement for dairy cows and other farm animals, and as a soil conditioner to garden center companies. “A dairy cow takes two ounces a day,” Morse said. “We have thousands of animals on our feed supplement.”
The granular meal is a green color, like the color of rockweed, the type of seaweed used in the process. “The coloration is what we're after,” Morse said. “We're able to do a very low temperature drying to get as high a quality as Iceland does with geothermal drying. All the Icelandic kelp meal has a nice green color. We're able to match that color.”
Iceland brings in 2,000 to 2,500 tons of this product annually through Portland harbor.
According to a University of Maine study Morse said there are a million tons of rockweed on the coast of Maine. Currently being harvested annually is around 1.4 percent or 14,000 tons. “The beds that we've harvested since 1971 have 30 percent more seaweed in them than when we started,” Morse said. “By properly cultivating the beds by harvesting the re-growth is increased.”
Morse said that with ocean acidification increasing, Bigelow Laboratory for Ocean Sciences has been documenting that rockweed harvesting is a good way to reduce the carbon, which would increase the alkalinity of the ocean. Properly harvesting the rockweed can help overcome the ocean acidification.
“We have a 16-inch cutting height,” he said. “Canada has a 10-inch cutting height. We have the highest cutting in all the five countries that harvest rockweed commercially. As a result, 25 percent of that million tons is in permanent conservation. There's not a fishery on the coast that has a more harvestable biomass, reserved continuously, than the rockweed fishery.”
Morse said there's a billion dollar market for seaweed, if the available seaweed was properly harvested and processed. “Right now 80 percent of our marine products are lobsters,” he said. “When I started in ’71, lobsters were around 10 percent. We need to develop some of the other fisheries.” Morse believes the seaweed industry could be bigger than the lobster one, unless lobster processing was brought back to Maine from Canada. “If they did that, instead of a 500 million dollar fishery, it would be a 2 ½ to 3 billion dollar fishery,” he said. “But for some reason we let New Brunswick process all our Maine lobster.”
Seaweeds have been used for fertilizer and food for thousands of years. The North American Kelp website states that “the northern New England coast is one of the more productive seaweed growing areas in the world. Its climate, over 3,000 miles of rocky habitat, abundance of nutrient-rich waters and a large tidal flow make it an ideal habitat for seaweeds.”
Morse said there was a forerunner to his seaweed business in the Boothbay area.
“Luther Maddox had a wood-fired rotary drum drier at Dogfish Head on Southport in the 1860s,” he said. “He was drying rockweed two miles from where I started, on Samoset Road, and making a soil conditioner and sending it to tobacco farmers in Connecticut. We built a wood-fired rotary drum seven years ago. I call it 'Back to the Future.’”
The company employs around 30 people and Morse said they would hire more. “We're open for multiple applications.”
North Atlantic Kelp also produces a line of liquid seaweed fertilizers.
Call 1-888-662-5357 for more information, or visit the website, http://www.noamkelp.com.
Event Date
Address
United States